Understanding rubber tracks – Features, types, and more
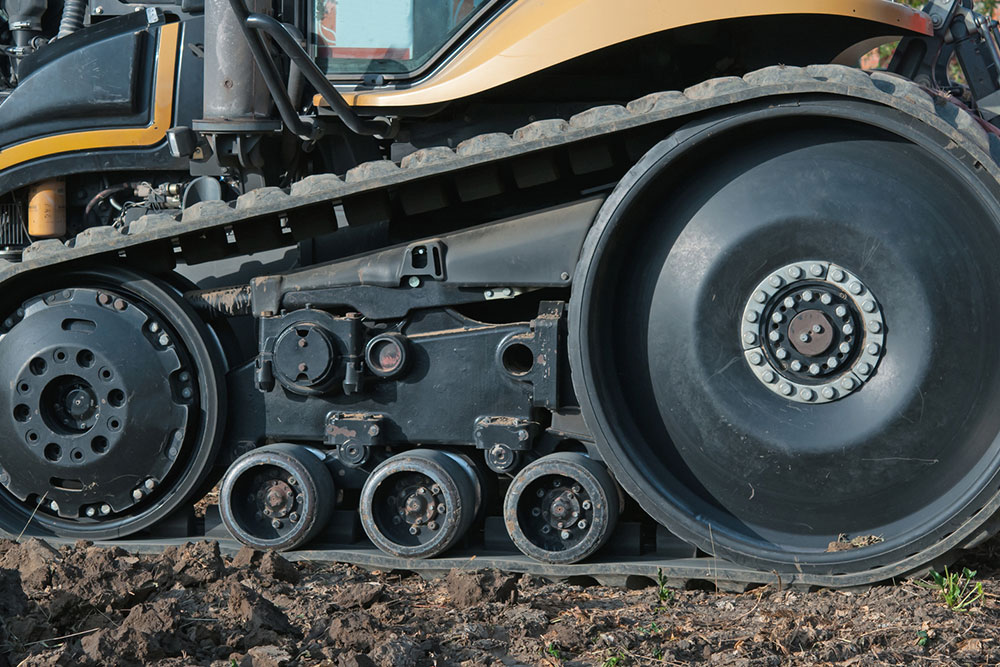
Rubber tracks are circular belts made of rubber added to machinery to maintain stability, high flotation, low ground pressure, and a smooth ride. They can be manufactured to suit a variety of scales, from large construction equipment to personal use machines such as mini skid steers, motorized wheelbarrows, and more. Read on to learn more about the features, uses, and types of rubber tracks, as well as how their replacements work.
Key features of rubber tracks
Not all rubber tracks are produced the same way. However, depending on the manufacturer and their intended use, these mechanical parts generally have all of the following features:
- Low ground connection and excellent traction force
- Optimizes traction system performance
- Delivers power efficiency
- Provides vehicles the ability to relocate (even on public roads) without causing any damage to the surroundings
Premium companies may strengthen these durable devices by using anti-cut rubber to increase durability, adding interlocking to reduce the risk of de-tracking and using anti-rust steel rods to minimize repairs.
Types of rubber tracks
Here are some of the most common types of rubber tracks that are manufactured and in use around the world:
Conventional rubber tracks
These tracks do not let the wheels come in contact with the metal guides and are allowed to be used only on undercarriages designed for rubber tracks.
Interchangeable rubber tracks
As the name suggests, these can be used interchangeably on undercarriages designed for steel or rubber tracks.
Rubber tracks with non-metal core (NMC)
These tracks are incredibly light, flexible, and made from a special rubber compound. Depending on their width and tread design, they also help ensure improved traction and reduced sinkage.
Rubber tracks for green area maintenance
These tracks are designed to maintain stability on steep slopes and protect the surrounding green area.
Anti-vibration rubber tracks (AV)
These tracks have a metal core, which helps reduce vibration. This, in turn, reduces track weight and vibration noise, allowing the vehicle to move smoothly.
Rubber tracks for agricultural machines
Agricultural rubber tracks have specifically been made to handle heavy and frequent usage, making them the most durable. When installed on tractors, Sowers, or other farm-related equipment, they can significantly help improve efficiency, as they improve tread surface area, can be used in wet weather conditions, and reduce fuel consumption.
Non-marking rubber tracks
Taking care of details such as markings is important when working on paved surfaces. These tracks are made from special rubber compounds to ensure minimum damage or marking during work.
Uses of rubber tracks
Rubber tracks are commonly used on machinery, such as:
Mini excavators
Owners can opt for tires or rubber tracks for equipment like mini excavators. Tracks can generally hold the machine’s weight better, making room to carry heavier loads of excavated material. They can also significantly reduce wear and tear compared to tires, allowing work to continue more efficiently.
Compact truck loader (CTL)
These large machines make use of heavy-duty rubber tracks to support their movement. The tracks allow the machine to move comfortably in tight spaces without significantly impacting the terrain around it.
Multi-terrain loaders (MTL)
These machines are used in areas where CTL may not be suitable, such as in challenging work conditions or delicate terrains. This requires special tracks, also known as tracked skid steers, as they offer better stability and grip and have a minimal ground impact during movement.
Apart from these, one can also find rubber tracks for snowmobiles, skid steers, snow groomers, earth-movers, skid loaders, and dump carriers.
Replacing rubber tracks
A rubber track’s lifespan varies significantly, with well-maintained ones serving anywhere between 1500 to 2000 working hours. However, to get the most out of the tracks, follow best practices such as regular checks and cleaning, correct tensioning, proper storage, and maintenance and lubrication of the undercarriage. Also, ensure that rubber tracks are replaced once worn or damaged. Constant loss of tension, cracked tracks, slipping tracks, and visible metal links are all signs that replacing the old rubber tracks is time. To install new ones, follow these steps:
- Begin by measuring their track width, longitudinal spacing (between the internal traction elements), and the number of teeth inside the track.
- Identify the type of rubber track required.
- Clear the workspace and wear protective equipment. Also, have the manual of the machine, sockets, a torch wrench, blocks of wood, a metal bar, and some grease handy. Depending on the size of the machine, a forklift may also be required.
- Next, lift the machine and empty its grease cylinder to reduce tension.
- Check if any idlers are supporting the track. Loosen these, and remove the old track from the sprocket.
- Inspect the undercarriage for wear and tear. In case of too much damage, have the machine repaired first.
- Install new sprockets and clean the contact surfaces of the drive motor.
- Now, place the new track properly and install it. Refill the grease cylinder to add tension. Additionally, ensure the track is not too tight, which may increase the wear risk.
- Move the track back and forward a few times to check if it has been attached properly, and secure the inspection hatch.
- Repeat as and when required.